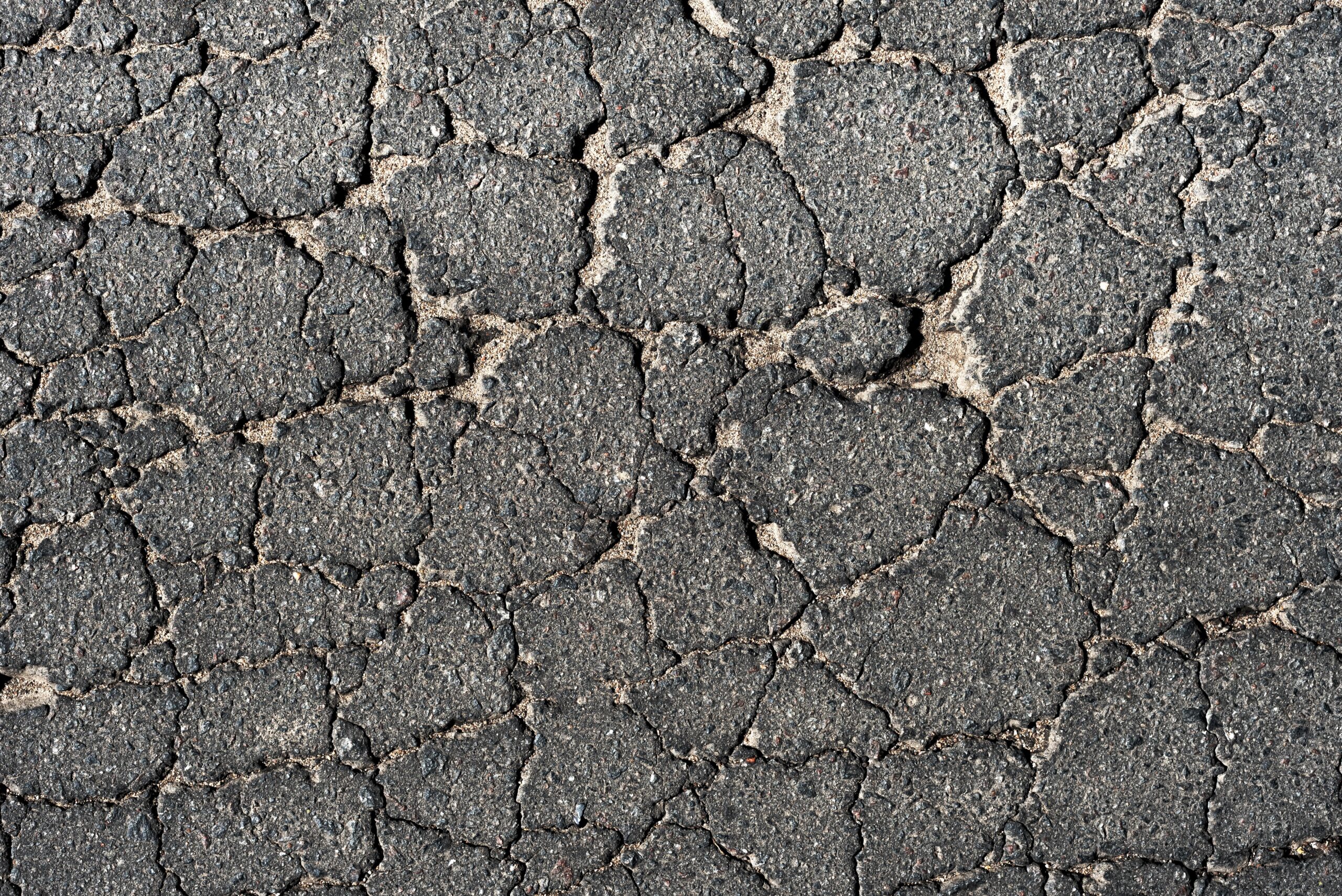
Winter in Denver transforms your commercial property into a battleground, where snow, ice, and biting cold test your concrete’s resilience. As a property manager, you’ve seen the toll: cracks widening, surfaces flaking, and repair bills soaring. Colorado’s freeze-thaw cycles and deicing salts are relentless, threatening parking lots and walkways with costly damage. But what if you could shield your concrete before winter strikes?
This guide unveils the best ways to prevent concrete damage in winter, offering practical, Colorado-focused strategies to save money, enhance safety, and keep your property pristine. Let’s fortify your concrete against the season’s wrath.
The Threat of Winter to Concrete
Winter is unforgiving to commercial concrete, especially in Colorado’s Front Range. The American Concrete Institute (ACI) warns that freeze-thaw cycles—over 150 annually in Denver—cause water in concrete pores to freeze, expand by 9%, and crack the surface. Deicing salts, widely used on parking lots, corrode reinforcement and trigger spalling. Snowplows scrape surfaces, while heavy traffic stresses already-weakened slabs. Without preventive measures, minor cracks can escalate into structural failures, costing thousands in repairs. The National Ready Mixed Concrete Association (NRMCA) estimates that proactive maintenance cuts winter-related repair costs by 60–80%.
Preventing damage requires understanding these threats and acting before winter sets in. By addressing vulnerabilities like cracks, poor drainage, and unprotected surfaces, you can extend your concrete’s lifespan and maintain a safe, professional property.
8 Best Ways to Prevent Concrete Damage in Winter
These carefully curated strategies, tailored for Colorado’s climate, protect your commercial concrete from winter’s harshest effects. Each is practical, research-backed, and designed for property managers seeking long-term solutions.
1. Apply a High-Quality Penetrating Sealant
Sealants are your concrete’s first line of defense. Penetrating sealants, like silane or siloxane-based products, soak into the concrete, forming a water-repellent barrier that resists freeze-thaw damage and salt penetration. In Colorado, where moisture from snowmelt is a constant threat, sealing every 3–5 years is critical, per ACI guidelines.
- How to Do It: Hire professionals to clean the surface, fill cracks, and apply sealant in fall, when temperatures are 50–80°F for optimal curing.
- Why It Works: Sealants reduce water absorption by up to 90%, preventing freeze-thaw cracking and salt corrosion.
- Pro Tip: Choose eco-friendly sealants to align with sustainable practices, a priority for many Denver businesses.
2. Repair Cracks Before Winter
Cracks are winter’s entry point for water and salts. Even hairline cracks (less than 1/8 inch) can widen during freeze-thaw cycles, compromising structural integrity. Filling cracks with flexible, polyurethane-based sealants in fall prevents water infiltration and further deterioration.
- How to Do It: Inspect for cracks wider than 1/16 inch. Clean debris with a wire brush or compressed air, then apply sealant using a caulking gun or professional equipment.
- Why It Works: Sealed cracks block moisture, reducing expansion damage by 70% (Concrete Construction Magazine).
- Pro Tip: For commercial lots, professional crack sealing ensures thorough application, especially in high-traffic areas.
3. Improve Drainage to Prevent Pooling
Standing water is a concrete killer in winter. Snowmelt or rain that pools on parking lots or walkways seeps into cracks, freezes, and causes spalling or slab settlement. In Denver, where spring snowmelt is heavy, proper drainage is non-negotiable.
- How to Do It: Ensure a 1–2% slope for runoff. Clear drains of debris before winter. Consider installing French drains or catch basins for chronic pooling areas.
- Why It Works: Effective drainage reduces water exposure, cutting freeze-thaw damage risk by 50%.
- Pro Tip: Inspect after storms to ensure drains remain clear, especially in low-lying Front Range properties.
4. Use Non-Corrosive Deicing Alternatives
Deicing salts like sodium chloride or calcium chloride are common in Colorado but wreak havoc on concrete. They penetrate surfaces, corrode rebar, and cause spalling. Switching to non-corrosive alternatives like calcium magnesium acetate (CMA) or sand protects your concrete.
- How to Do It: Stock CMA or sand for winter use. Apply sparingly to icy areas, avoiding over-application near concrete.
- Why It Works: CMA is 80% less corrosive than traditional salts, preserving surface integrity (NRMCA).
- Pro Tip: Educate staff on proper deicer use to prevent accidental damage to walkways or parking spaces.
5. Clear Snow and Ice Promptly
Accumulated snow and ice increase moisture exposure, seeping into cracks or joints as they melt. Snowplows, while necessary, can scrape unprotected surfaces, causing pitting. Prompt snow removal minimizes these risks and enhances safety.
- How to Do It: Shovel or plow snow within 24 hours of snowfall. Use plastic-edged shovels or adjust plow blades to avoid surface damage.
- Why It Works: Quick removal reduces water infiltration, preventing freeze-thaw cycles from weakening concrete.
- Pro Tip: Apply a thin layer of sand for traction after clearing to avoid chemical deicers.
6. Maintain Expansion Joints
Expansion joints allow concrete slabs to move with temperature changes, but deteriorated or debris-filled joints lose effectiveness. In Denver’s fluctuating winter climate, compromised joints lead to slab cracking or shifting as water seeps beneath.
- How to Do It: Inspect joints in fall. Remove old sealant or debris with a screwdriver, then refill with flexible silicone or polyurethane sealant.
- Why It Works: Intact joints reduce slab stress, preventing cracks by up to 60%.
- Pro Tip: Check joints after snowplowing, as blades can dislodge sealant in high-traffic lots.
7. Limit Heavy Traffic During Thaws
Winter thaws, common in Colorado’s sunny January days, soften the subbase beneath concrete, making it vulnerable to cracking under heavy loads. Delivery trucks or construction vehicles can exacerbate damage in these conditions.
- How to Do It: Restrict oversized vehicles during thaws (temperatures above 32°F after freezes). Post signs or reroute traffic to reinforced areas.
- Why It Works: Reducing load stress preserves subbase stability, cutting crack risk by 40%.
- Pro Tip: For unavoidable heavy traffic, reinforce weak areas with temporary mats or consult professionals for slab strengthening.
8. Schedule Pre-Winter Inspections
A thorough inspection in late fall identifies vulnerabilities like cracks, spalling, or drainage issues before winter amplifies them. For commercial properties, where safety and uptime are critical, proactive assessments are essential.
- How to Do It: Walk your lot with a checklist, noting cracks, uneven slabs, or pooling areas. Hire professionals for a detailed evaluation, including subbase analysis.
- Why It Works: Early detection allows timely repairs, saving 60–80% compared to post-winter fixes (Concrete Construction Magazine).
- Pro Tip: Document findings with photos to track changes and prioritize repairs, especially for large Denver retail lots.
Why Winter Prevention Is Critical in Colorado
Colorado’s winter is uniquely brutal for concrete. Denver’s high altitude intensifies UV exposure, drying surfaces and making them brittle. Over 150 freeze-thaw cycles stress concrete pores, while deicing salts—used on 70% of commercial lots—accelerate corrosion. Snowplows and heavy traffic add mechanical wear, particularly in busy areas like strip malls or warehouses. The NRMCA notes that unprotected concrete can lose 20–30% of its strength in a single harsh winter. Preventive measures, implemented before snow falls, protect your investment, reduce liability, and maintain a professional appearance for customers.
Timing Your Preventive Efforts
Fall is the optimal time for winter preparation, ideally September or October in Colorado, when temperatures support sealant curing and repairs. Avoid maintenance during sub-freezing conditions or heavy snow, as cold hinders adhesion, and moisture compromises results. For ongoing protection, schedule biannual inspections (fall and spring) to catch new issues. High-traffic lots may need monthly checks during winter to monitor snowplow damage or deicer effects. Acting early ensures your concrete withstands the season’s challenges.
Prevention vs. Repair: The Cost Advantage
Preventive maintenance is far more cost-effective than post-winter repairs. The ACI estimates that sealing and crack repairs cost $2–$10 per square foot, while slab replacement can exceed $50 per square foot. A 10,000-square-foot parking lot could face $500,000 in replacement costs versus $20,000–$100,000 for prevention and minor repairs. By investing in sealants, drainage improvements, and inspections, you avoid safety hazards, ADA violations, and business disruptions, all while extending your concrete’s 20–30-year lifespan.
Frequently Asked Questions
1. How frequently should I seal concrete to prepare for winter?
Concrete should be sealed every 3 to 5 years, depending on environmental exposure and usage levels. High-traffic commercial lots may require sealing every 2 to 3 years to maintain optimal protection against moisture and deicing chemicals.
2. Is rock salt safe for use on concrete surfaces?
No. Rock salt (sodium chloride) accelerates corrosion, leading to surface spalling and structural deterioration. Instead, use safer alternatives like calcium magnesium acetate or sand to maintain traction without harming the concrete.
3. How soon should snow be removed after a storm?
Snow should be cleared within 24 hours of accumulation. Prompt removal limits moisture penetration and prevents the formation of ice, which expands and contracts within concrete, leading to cracks.
4. When is the best time to seal or repair concrete before winter?
Late summer through early fall is ideal. Daytime temperatures between 50°F and 80°F allow sealants and repair materials to cure properly before freezing conditions set in.
5. Can I handle winter concrete maintenance on my own?
Minor tasks like debris removal and light cleaning can be managed in-house. However, professional services are strongly recommended for sealing, crack repair, and drainage improvements to ensure long-term durability and compliance with industry standards.
6. What are the risks of skipping winter protection?
Neglecting winter preparation can lead to significant damage, including cracking, surface flaking, and slab displacement. These issues often require major repairs or full replacement—at a cost five to ten times higher than routine preventative maintenance.
Stay Ahead of Winter: Protect Your Concrete Investment
Colorado winters are unforgiving, and your commercial concrete services, surfaces face daily threats from ice, snow, and harsh deicing chemicals. Without proper preparation, even small cracks can escalate into major structural problems. By taking proactive steps—sealing, timely repairs, safe snow removal, and the use of non-corrosive deicers—you protect your investment, reduce liability, and ensure safe access for everyone.
Prepare now to prevent costly repairs later. Schedule a fall inspection at asphaltcoatingscompany and give your concrete the protection it needs to weather the season.