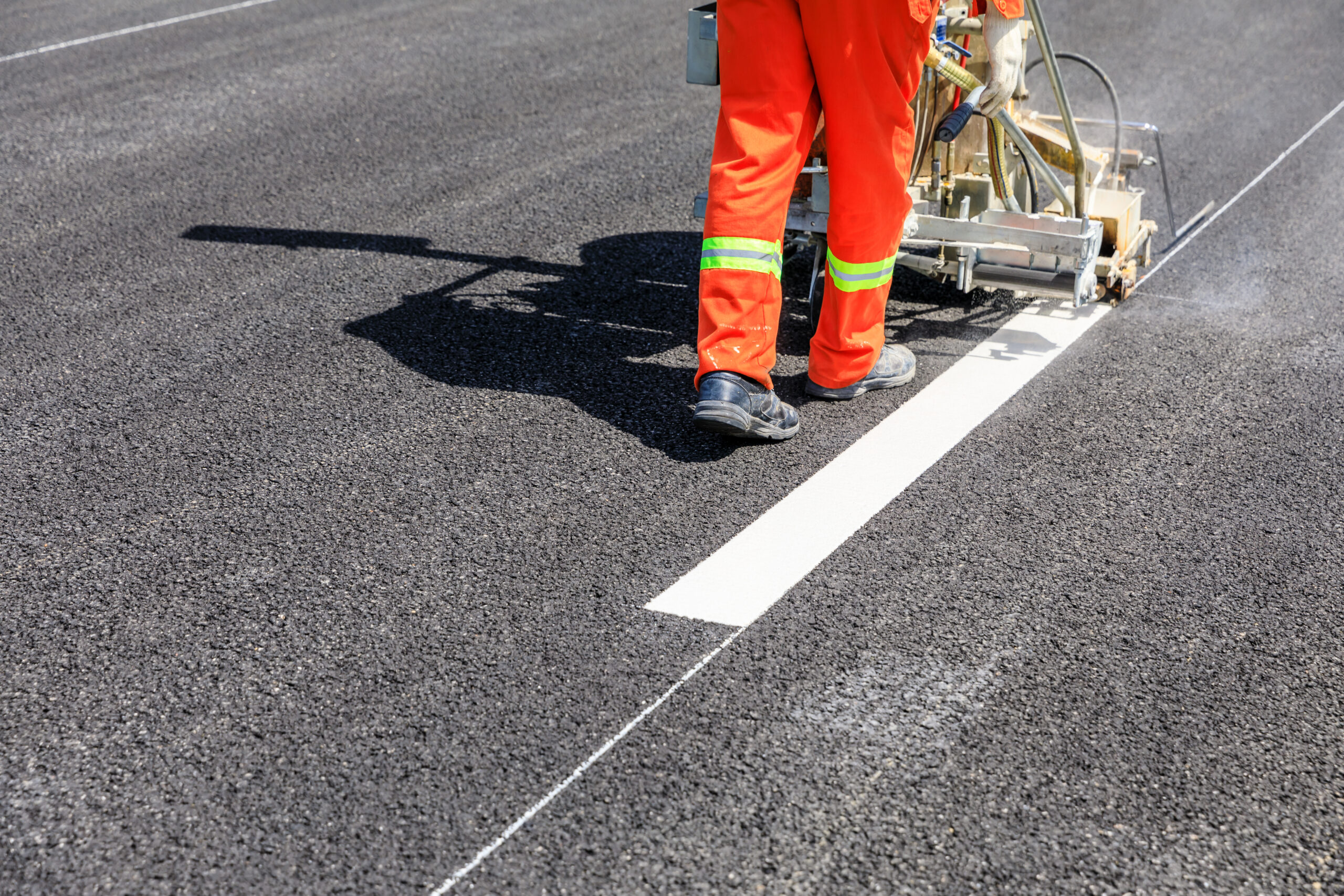
A smooth asphalt surface adds serious value to your property. It enhances curb appeal, improves safety, and can even help your business make a positive first impression. However, without regular upkeep, the same surface begins to crack, fade, or deteriorate, ultimately leading to costly repairs in the long run.
The good news is that yearly asphalt maintenance doesn’t have to be complicated. Whether you manage commercial properties, oversee a business campus, or own an apartment complex, a simple and strategic plan can save you thousands in repairs while extending the life of your investment.
In this guide, you’ll learn how to create and maintain a yearly asphalt maintenance plan that’s easy to follow, effective, and budget-friendly.
Why Yearly Asphalt Maintenance Planning Matters
Asphalt can last up to 25 years when properly maintained. Consistent maintenance can reduce repair costs by as much as 30%, according to national industry data. That’s not just peace of mind. It’s thoughtful financial planning.
Benefits of a Year-Round Maintenance Plan
- Extends pavement life by lasting 15 to 25 years or more with proper maintenance.
- Improves safety by reducing trip hazards and potholes.
- Boosts appearance by maintaining a clean, blacktop look.
- Minimizes liability risks, especially in commercial parking lots and walkways.
- Helps control costs by preventing emergency repairs and long-term degradation.
Planning also gives you the flexibility to choose the right contractors, products, and timing without scrambling during peak construction seasons or adverse weather conditions.
Step 1: Assess Your Asphalt’s Condition
Before creating any plan, take inventory of your asphalt’s current condition. This step helps you prioritize tasks and estimate cost and urgency.
How to Conduct an Assessment
- Inspect for cracks, potholes, discoloration, oil stains, or drainage issues.
- Look for surface erosion or soft spots at the edges.
- Use photo documentation to track wear over time.
- Rate the surface using the PASER system (1-10) or refer to a checklist from the Asphalt Institute.
- Walk the lot after rainfall to identify pooling or drainage problems.
Consider hiring a professional inspector to catch sub-surface or structural issues early.
Step 2: Identify Maintenance Needs
With your assessment in hand, list what your pavement needs, both immediate and preventive.
Immediate Repairs (Do These First)
- Patching potholes
- Filling large cracks (greater than ¼ inch)
- Fixing drainage or grading issues
Preventive Maintenance Tasks
- Crack sealing
- Sealcoating
- Cleaning and sweeping
- Routine inspections
Consider These Factors
- Asphalt age: Newer asphalt may just need sealcoating. Older surfaces (10+ years) often require minor repairs.
- Traffic volume: High-use areas wear down faster.
- Environmental exposure: Tree roots, water runoff, or shade can accelerate wear and tear on the surface.
Step 3: Create a Seasonal Maintenance Schedule
Weather affects how asphalt is worn and which tasks can be done effectively—schedule work by season to stay ahead of issues.
Spring (March to May)
- Assess winter damage
- Fill cracks
- Schedule sealcoating in late spring
Summer (June to August)
- Watch for heat-related soft spots
- Deep-clean oil or tire stains
- Clear drains to prepare for storms
Fall (September to November)
- Inspect after summer traffic
- Complete minor surface repairs
- Apply final sealcoating before cold sets in
Winter (December to February)
- Focus on surface safety (de-icing, debris removal)
- Handle emergency freeze-thaw damage.
- Review and update your maintenance plan and budget.
Book primary services in spring or fall when contractor availability is higher and prices are more favorable.
Step 4: Budget for Maintenance
Unexpected costs are the number one reason maintenance gets delayed. With a clear plan, budgeting becomes predictable.
Estimated Costs for Common Tasks
- Sealcoating: $0.20–$0.45 per square foot
- Crack sealing: $1–$2 per linear foot
- Pothole patching: $100–$500 each
- Resurfacing or overlays: Varies by project size and region
How to Plan Financially
- Use online tools like Asphalt Kingdom’s Blacktop Calculator
- Establish an annual maintenance fund.
- Add a 10% buffer for rising material costs or emergencies.
Step 5: Establish a Routine Maintenance Cycle
Not every task needs to happen every year. Use a rotating cycle to maximize value and avoid redundancy.
Suggested 3-Year Maintenance Cycle
- Year 1: Sealcoating to shield from the sun and water
- Year 2: Crack sealing to prevent joint expansion
- Year 3: Repairs and overlays to correct structural or drainage issues
Guidelines for Best Results
- Never delay sealcoating beyond 3 years.
- Address small cracks annually if needed.
- Use rubberized materials for better patch longevity.
Step 6: Know When to Call Professionals
While some tasks can be done as a DIY project, larger repairs or resurfacing are best left to professionals.
Hire a Pro For:
- Pothole repairs
- Milling and overlays
- Full-depth patching
- Specialty inspections (ADA compliance, sub-base, drainage)
Benefits of Working with Experts
- The right products for your climate
- Cleaner, longer-lasting results
- Compliance with local codes
- Faster completion with less disruption
Professionals also help you catch minor issues before they turn into significant costs, especially on large or high-traffic properties.
Step 7: Monitor and Adjust Your Plan Over Time
An innovative maintenance plan is flexible. As conditions change, so should your approach.
How to Keep Your Plan Effective
- Track tasks and inspections
- Conduct quarterly reviews, especially after seasonal changes.
- Monitor wear patterns and adjust strategies as needed.
- Keep a logbook with notes, photos, and contractor quotes.
This documentation fosters transparency and can even enhance resale value by providing a clear record of maintenance history.
What Are The Common Mistakes to Avoid
Avoid these pitfalls to keep your plan efficient and your asphalt in good shape:
Top 5 Mistakes
- Ignoring small cracks that widen with weather
- Overlooking standing water in drainage areas leads to faster failure.
- Using expired or poor-quality materials
- Hiring unqualified contractors for complex work
- Sealing in cold or rainy conditions, which ruins adhesion
Smart Planning Saves Thousands
A property manager in Texas partnered with a local logistics provider to maintain a 150-space parking lot. In early spring, they:
- Conducted a thorough inspection with a custom checklist
- Scheduled sealcoating and repairs in manageable phases
- Used high-quality fillers delivered on-site to reduce downtime
- Spread out work over the year for smoother budgeting.
They extended the lot’s lifespan by 10 years and saved over $10,000 in potential replacement costs.
Easy Yearly Asphalt Maintenance Plan
Follow this simple yearly maintenance schedule to keep your asphalt looking great and extend its lifespan:
Task | Frequency | Details |
Inspect Asphalt | Monthly | Check for cracks, potholes, and drainage issues |
Sealcoating | Every 3 years | Apply in spring/fall between 50–90°F |
Crack Sealing | Every 3 years | Fill cracks over ¼ inch with rubberized filler |
Repairs | As needed | Patch potholes, fix drainage or surface issues |
Cleaning | Monthly | Sweep debris, treat stains, clear gutters and drains |
Budgeting | Annually | Set funds with a 10% buffer for unexpected costs |
Frequently Asked Questions
How often should I schedule asphalt maintenance to keep my pavement in good condition?
It’s best to inspect your asphalt surfaces at least once a year. Schedule sealcoating every 2 to 3 years and perform crack sealing as needed, typically every 3 years or sooner if the damage is observed.
What are the key steps in creating an effective yearly asphalt maintenance plan?
Start by assessing the current condition of your pavement. Then, prioritize immediate repairs, set seasonal maintenance tasks such as sealcoating and crack sealing, budget annually, and track your progress throughout the year.
Why is sealcoating essential, and when is the best time to apply it?
Sealcoating protects asphalt from UV rays, moisture, and chemical spills. Apply it during dry conditions with temperatures above 50°F, ideally in late spring or early fall, for best adhesion and durability.
How can I identify cracks or damage that need immediate repair?
Watch for cracks wider than ¼ inch, potholes, signs of drainage failure, and soft or crumbling areas. Addressing these early prevents water infiltration and more serious structural damage.
What are the common mistakes I should avoid in asphalt maintenance?
Avoid skipping routine care, using poor-quality materials, neglecting drainage design, sealing in cold or wet weather, and hiring unqualified contractors for structural repairs.
When should I hire a professional for asphalt maintenance instead of doing it myself?
Hire professionals for large-scale work such as pothole patching, milling, and overlays or when compliance and long-term durability are essential, especially in high-traffic or commercial areas.
Make Maintenance Easy with Trusted Help
Planning your yearly asphalt maintenance doesn’t have to be a headache. Break it into manageable steps: assess your surface, prioritize needs, schedule by season, set a realistic budget, and follow a smart cycle. With the right strategy, your pavement will last longer, look better, and require fewer emergency repairs.
To get started the easy way, contact Asphalt Coatings Company for expert advice, timely service, and free estimates that keep your maintenance plan on track.