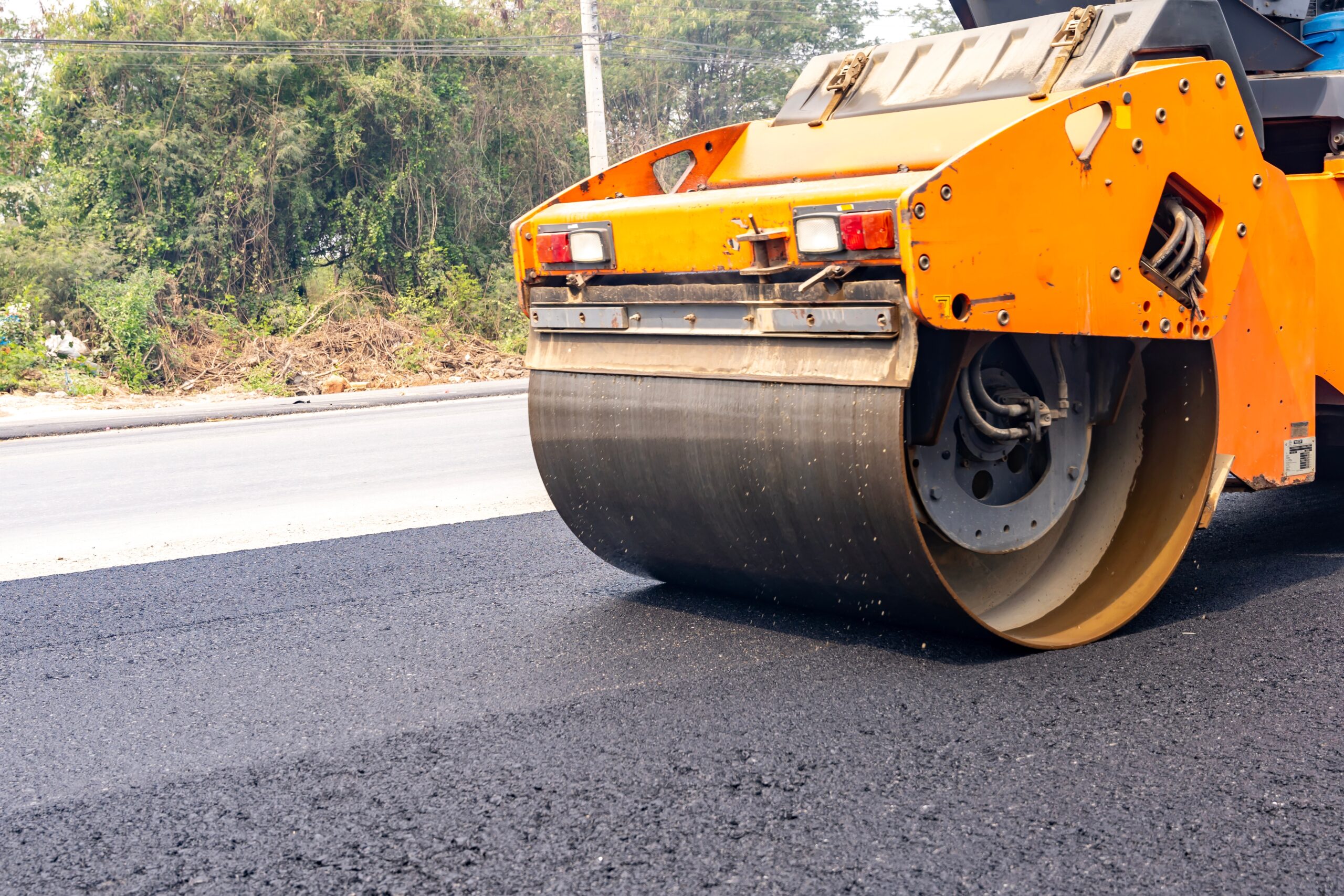
Creating a durable asphalt surface—whether a parking lot, driveway, or roadway—requires more than just paving equipment and materials. Successful asphalt construction hinges on thoughtful planning, proper site preparation, and choosing an experienced contractor.
This guide outlines the crucial steps you need to take to ensure your property is construction-ready, providing insights into drainage, permitting, grading, and more. By partnering with Asphalt Coatings Company, you’ll avoid costly pitfalls and ensure your investment stands the test of time.
Defining the Scope and Purpose of Your Asphalt Project
Before diving into new construction, it’s essential to identify your property’s unique requirements. Understanding the type of asphalt surface you need and how it will be used helps determine the structural specifications, regulatory needs, and environmental considerations.
Understanding Project Type and Load Requirements
The structural requirements for a light-use residential driveway differ significantly from those of a commercial parking lot designed for heavy vehicles.
By defining whether your asphalt surface will accommodate light foot traffic, passenger cars, or heavy-duty vehicles, you help your contractor design the right thickness and base materials.
Aligning Design with Regulatory and Accessibility Standards
Incorporating zoning laws, ADA accessibility standards, and fire access requirements from the planning phase is crucial. This ensures that your asphalt surface not only performs well but also meets municipal and federal compliance benchmarks.
Addressing Colorado’s Climate Considerations
In regions like Colorado, extreme temperature swings and freeze-thaw cycles pose challenges for asphalt integrity. Selecting climate-appropriate materials and design features—such as moisture-resistant base layers and adequate drainage—protects your pavement from early deterioration.
Evaluating the Site for Construction Readiness
Site evaluation forms the backbone of any construction project. This process ensures that the land can support the asphalt layers and that key environmental and structural issues are addressed beforehand.
Assessing Soil Strength and Composition
A geotechnical analysis reveals the soil’s load-bearing capacity. If the soil is weak, expansive, or overly moist, it may need to be stabilized or replaced. Ignoring this step could result in long-term structural failure.
Understanding Site Topography and Drainage Flow
Understanding how water flows across your property allows contractors to engineer slopes and grading strategies that channel water away from the surface. Proper topography planning prevents erosion and pothole development.
Clearing, Grading, and Subbase Installation
Once your site is deemed suitable for construction, the physical preparation begins. Clearing the area, shaping the terrain, and laying the subbase are essential to building a strong, resilient foundation.
Removing Existing Pavement and Vegetation
All previous pavement, organic matter, and debris must be removed to create a clean base. Retaining old or deteriorated materials can affect bonding and reduce the overall longevity of the asphalt surface.
Precision Grading for Water Runoff and Stability
Grading isn’t just about making the surface level; it’s about strategically angling the surface to manage water runoff. Proper grading ensures that water flows into drains or landscaping, not into the base layers of your pavement.
Installing and Compacting the Subbase
A compacted subbase of crushed aggregate or recycled material distributes weight evenly and prevents surface deformities. It must be laid and compacted in layers to achieve at least 95% compaction density, providing a solid support structure for the asphalt above.
Infrastructure Planning and Legal Compliance
Ignoring utility infrastructure and legal compliance can delay your project and lead to fines or reconstruction. Planning around these elements saves time and resources.
Locating and Protecting Underground Utilities
Contact local utility providers to identify buried lines. Marking gas, water, and electrical lines prevents damage and ensures worker safety during excavation and paving.
Obtaining Permits and Meeting Inspection Requirements
Your project must meet local, state, and sometimes federal construction regulations. Asphalt Coatings Company handles permitting, plan submissions, and mandatory inspections to keep your project on schedule.
Environmental and ADA Compliance Integration
Designing for stormwater management and accessibility from the beginning ensures your project passes environmental reviews and ADA inspections without surprises.
Communicating with Stakeholders and Managing Logistics
Effective communication and smart scheduling make construction more efficient and less disruptive, especially for active commercial sites.
Informing Tenants, Staff, and Visitors in Advance
Post signs, send out notices, and provide alternate access routes in advance. This fosters goodwill and prevents confusion during construction.
Planning Construction Timing to Minimize Disruption
Schedule paving work during off-hours, weekends, or holiday breaks when traffic is low. Asphalt Coatings Company offers phased installations and flexible scheduling to accommodate your business needs.
Executing the Paving Phase Efficiently
With the groundwork in place, the actual Asphalt paving in Colorado can begin. This is where technical precision and proper equipment usage are vital.
Material Delivery and On-Site Equipment Staging
Ensure that all asphalt mix and machinery are on-site and ready before paving starts. Delays in this phase can affect the asphalt’s temperature and bonding strength.
Layered Asphalt Installation and Compaction
Paving is done in layers called lifts. Each lift is compacted using vibratory rollers to eliminate air pockets and strengthen structural cohesion. Failure to compact properly can lead to soft spots and premature surface failure.
Maintaining Quality Control and Supervision
Every step should be monitored closely—temperature, compaction pressure, and thickness. Asphalt Coatings Company maintains constant quality checks to ensure the job meets durability and safety standards.
Post-Paving Processes and Client Handover
Even after the asphalt is laid, the process isn’t over. Post-paving steps help transition the surface into usable condition and complete the project.
Curing and Load Restrictions
Curing typically takes 24–48 hours for light use and up to 30 days for full hardening. Avoid placing heavy equipment or turning vehicle wheels sharply during this period.
Painting Lines and ADA-Required Markings
Proper striping maximizes efficiency and safety. Use reflective, high-durability paints for line markings, ADA zones, arrows, and pedestrian walkways.
Final Walkthrough and Site Sign-Off
Before final handover, perform a detailed inspection. Any imperfections are addressed immediately to ensure client satisfaction and compliance with project specs.
Maintenance Planning for Long-Term Performance
Your asphalt’s longevity depends on a proactive maintenance approach. Investing in upkeep protects your initial construction investment.
Routine Seal Coating and Crack Filling
Seal coating every 2–3 years protects the surface from UV rays, water, and chemicals. Crack sealing prevents moisture from reaching the subbase and causing major damage.
Annual Site Inspections and Surface Cleaning
Inspections help catch problems early. Cleaning the surface regularly removes oil and debris that degrade asphalt over time.
Maintenance Contracts with Asphalt Coatings Company
ACC provides custom maintenance programs that include inspections, repairs, and preventive treatments tailored to your property’s usage and traffic load.
Avoiding Pitfalls in Preparation and Planning
Even the best paving materials can fail if basic prep steps are skipped. Here are the most common mistakes to avoid.
Neglecting Soil and Drainage Requirements
Failing to stabilize weak soil or plan for drainage often results in surface failure. Always include geotechnical and grading assessments.
Proceeding Without Legal Permits
Unpermitted projects can be halted mid-process and cost thousands in fines or corrections. Ensure every step is documented and approved.
Cutting Corners on Base Installation
Rushing or skimping on the base material leads to soft spots, potholes, and costly repairs. Always follow best practices in subbase compaction.
Cost Planning and Value Optimization
Budgeting accurately ensures you can complete your project without compromising on quality. Understanding where costs originate helps you make informed decisions.
Factor | Impact on Cost | Notes |
Site Size & Scope | Higher square footage increases costs | More materials and labor required |
Soil and Grading Complexity | Poor soil or steep slopes add prep time | May require stabilization or cut/fill efforts |
Asphalt Thickness & Mix Type | Thicker layers and premium mixes cost more | Must match load and climate requirements |
Permits and Compliance | Legal documentation adds upfront costs | Avoids fines and reconstruction |
Weather Delays | Seasonal or unexpected weather may delay work | Buffer scheduling and budget accordingly |
Planning for Contingencies
Set aside 10–15% of your total budget for unforeseen conditions like bad weather or unexpected subsurface conditions.
Evaluating Long-Term ROI
A well-built asphalt surface can last 20–30 years with maintenance, increasing property value and minimizing long-term costs.
Build With Confidence
Proper preparation is the cornerstone of successful asphalt construction. From understanding soil quality to planning for weather, drainage, and accessibility, every step contributes to the life and performance of your pavement.
Asphalt Coatings Company brings over three decades of experience to ensure each project meets the highest standards. Reach out today for a customized consultation and a no-obligation quote.
Frequently Asked Questions
How long does asphalt construction typically take from start to finish?
Most commercial projects range from 2 to 5 days, depending on scope and weather.
Can I remain open for business during asphalt installation?
Yes. Work can be phased or scheduled during off-hours to minimize disruption.
What are the signs that my existing asphalt needs full replacement?
Extensive cracking, sinking, and water damage often indicate that full-depth reconstruction is necessary.
How do I know if my property needs regrading before paving?
Pooling water or uneven terrain are key signs your property may need slope correction before paving.
Is asphalt paving environmentally sustainable?
Yes. Asphalt is recyclable, and many mixes are made with reclaimed materials, reducing environmental impact.