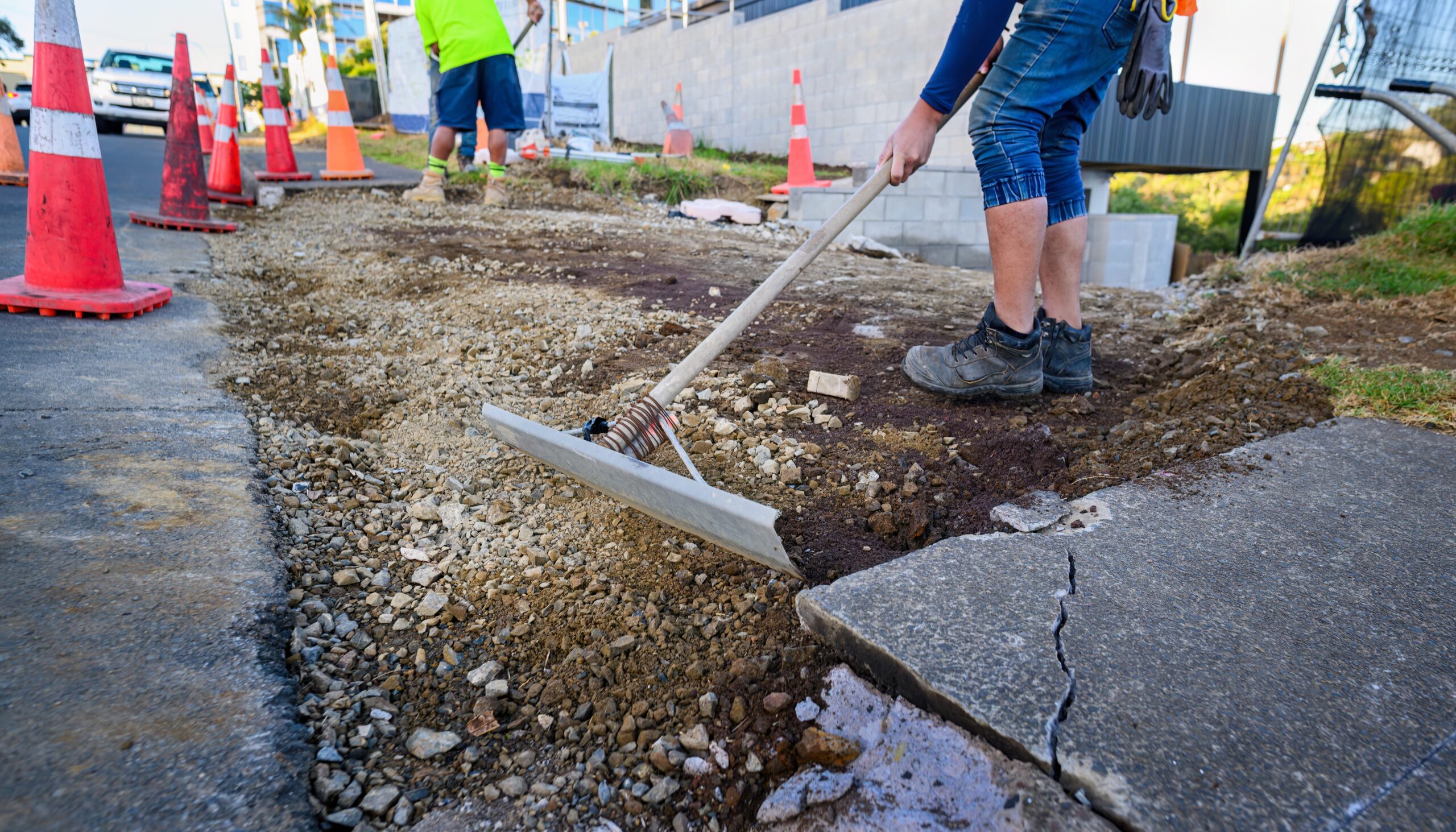
Imagine walking across your commercial parking lot in Denver, where winter’s bite and summer’s blaze test every surface. You notice a jagged crack snaking through the concrete, or a rough, crumbling patch underfoot.
These aren’t just eyesores, they’re warnings of deeper damage that could disrupt your business and dent your budget. In Colorado’s unforgiving climate, commercial concrete faces unique challenges, from freeze-thaw cycles to deicing salts.
Ignoring early signs risks costly repairs or safety hazards. This guide reveals the key indicators your concrete needs repair, empowering you to act swiftly and keep your property safe and inviting.
Why Commercial Concrete Maintenance Matters
Concrete is the backbone of commercial properties, forming parking lots, walkways, and loading zones that endure heavy traffic and harsh weather. Unlike residential surfaces, commercial concrete faces constant stress from vehicles, foot traffic, and environmental factors.
The American Concrete Institute (ACI) notes that untreated damage in concrete can lead to structural failure, increasing repair costs by up to 70% if ignored. In Colorado, where Denver’s freeze-thaw cycles and high-altitude UV rays accelerate wear, timely repairs prevent minor issues from escalating into major liabilities, ensuring safety, compliance, and a professional appearance.
7 Signs Your Commercial Concrete Needs Repair
Your concrete sends clear signals when it’s in distress. Here are seven critical signs to watch for, each tied to Colorado’s unique conditions.
1. Visible Cracks Wider Than 1/8 Inch
Cracks are the most obvious sign of concrete damage. Hairline cracks (less than 1/8 inch) are often cosmetic, but wider cracks indicate stress from traffic, temperature shifts, or settling. In Denver, freeze-thaw cycles cause water to seep into cracks, freeze, and expand, widening them further. These “structural cracks” can compromise the slab’s integrity.
- What to Check: Inspect for cracks you can fit a credit card into. Linear or diagonal cracks are especially concerning.
- Why It Matters: Wide cracks allow water and debris to penetrate, eroding the subbase and leading to slab failure.
2. Spalling or Flaking Surfaces
Spalling occurs when the concrete surface flakes or peels, often due to freeze-thaw damage or deicing salts. In Colorado, where road salts are common, these chemicals penetrate concrete, corroding reinforcement and causing the surface to pit or crumble. Spalled concrete looks rough and uneven, posing trip hazards.
- What to Check: Look for pitted, scaly patches, especially in high-traffic areas like walkways or near entrances.
- Why It Matters: Spalling weakens the concrete’s surface, accelerating deterioration and requiring urgent repair.
3. Uneven or Sunken Slabs
If your parking lot or walkway feels uneven, you may have sinking slabs, often caused by soil settlement or erosion beneath the concrete. In the Front Range, heavy spring snowmelt can wash away subbase material, leaving voids that cause slabs to sink or tilt. Uneven surfaces create safety risks and accessibility issues.
- What to Check: Use a level or observe if water pools unevenly. Check for slabs that tilt or wobble underfoot.
- Why It Matters: Sunken slabs can cause trips or vehicle damage, and untreated voids lead to further cracking.
4. Water Pooling or Poor Drainage
Standing water after rain or snowmelt signals drainage issues, often linked to cracks, uneven slabs, or poor grading. In Denver, where sudden storms are common, pooling water seeps into concrete, weakening it and promoting further cracking. The NRMCA warns that prolonged water exposure can reduce concrete strength by 20–30%.
- What to Check: After precipitation, note areas where water collects for over an hour. Look for nearby cracks or low spots.
- Why It Matters: Poor drainage accelerates damage, especially in freeze-thaw conditions, and creates slippery surfaces.
5. Discoloration or Staining
Concrete that’s discolored, often gray, yellow, or stained, may indicate chemical damage or efflorescence, a white, powdery deposit caused by water leaching salts to the surface. Oil spills from vehicles or deicing salts in commercial lots can penetrate unprotected concrete, causing stains and softening the material.
- What to Check: Look for persistent stains or white patches, especially in parking spaces or near loading zones.
- Why It Matters: Stains signal reduced chemical resistance, while efflorescence indicates moisture issues that weaken the slab.
6. Popouts or Surface Pitting
Popouts are small, conical holes where aggregate pieces break away from the surface, often due to freeze-thaw cycles or poor-quality materials. In Colorado, where moisture infiltrates concrete during winter, freezing water pushes out aggregate, leaving pits. These defects worsen over time, creating rough, unsafe surfaces.
- What to Check: Inspect for small, shallow holes (1–2 inches wide) scattered across the surface, especially in older concrete.
- Why It Matters: Popouts indicate material degradation, increasing the risk of larger spalling or cracking.
7. Joint Deterioration or Widening
Expansion joints between concrete slabs allow for thermal movement, but when they widen, crumble, or fill with debris, they lose effectiveness. In Denver’s fluctuating climate, joints deteriorate faster due to temperature swings and salt exposure, allowing water to seep beneath slabs and erode the subbase.
- What to Check: Examine joints for gaps wider than 1/4 inch, crumbling sealant, or debris buildup.
- Why It Matters: Deteriorated joints lead to slab movement, cracking, and instability, requiring immediate repair.
Causes of Commercial Concrete Damage in Colorado
Understanding why your concrete is failing helps prioritize repairs. Key causes include:
- Freeze-Thaw Cycles: Denver’s 150+ freeze-thaw cycles annually cause water in concrete to expand and contract, cracking or spalling the surface (NRMCA).
- Deicing Salts: Common in commercial lots, salts corrode reinforcement and degrade surface integrity.
- Heavy Traffic: Delivery trucks and constant foot traffic stress concrete, especially in poorly designed slabs.
- UV Exposure: Colorado’s high-altitude sun accelerates surface drying, making concrete brittle.
- Subbase Issues: Poor compaction or erosion beneath slabs causes settling or cracking.
- Aging Concrete: Most commercial concrete lasts 20–30 years with maintenance. Beyond that, repairs are critical.
Addressing these factors through timely repairs prevents escalation and extends service life.
When to Act: Timing and Conditions
Concrete repairs are most effective when damage is caught early. The ACI recommends addressing cracks wider than 1/8 inch or spalling deeper than 1/4 inch immediately. In Colorado, spring and fall are ideal for repairs, as temperatures between 50–80°F ensure proper curing of sealants and patching materials. Avoid repairs during heavy rain or sub-freezing conditions, which hinder adhesion.
Schedule biannual inspections, especially after winter snowplowing or summer storms, to identify new damage. For high-traffic lots, monthly walkthroughs help catch issues early. Concrete Construction Magazine estimates that early repairs cost 60–80% less than full slab replacement.
Types of Concrete Repairs
Not all damage requires the same fix. Common repair methods include:
- Crack Sealing: Fills cracks with flexible sealants to block water. Best for structural cracks.
- Patching: Repairs spalling or popouts with cement-based compounds. Ideal for localized damage.
- Slab Lifting: Injects foam or grout to raise sunken slabs. Used for uneven surfaces.
- Joint Repair: Replaces deteriorated joint sealant to restore flexibility.
- Overlay: Applies a thin concrete layer for widespread surface damage. Less common but effective.
- Replacement: Removes and replaces severely damaged slabs. A last resort.
Assess your concrete’s condition to choose the right repair, or consult a professional for a comprehensive evaluation.
Prevention Tips to Protect Your Concrete
Preventive maintenance reduces repair frequency. Try these strategies:
- Seal Regularly: Apply a penetrating sealant every 3–5 years to repel water and chemicals.
- Clean Spills Promptly: Remove oil or fuel spills immediately to prevent softening.
- Improve Drainage: Ensure proper grading or install drains to divert water.
- Use Salt Alternatives: Opt for sand or non-corrosive deicers to protect concrete.
- Limit Heavy Loads: Restrict oversized vehicles or reinforce slabs for truck traffic.
- Inspect Routinely: Check for early signs of wear biannually to catch issues before they worsen.
These steps, paired with timely repairs, keep your concrete durable and safe.
Frequently Asked Questions
How often should commercial concrete surfaces be inspected?
For optimal results, inspections should be conducted twice a year, ideally in spring and fall, to identify damage from seasonal changes. High-traffic areas may benefit from monthly visual checks to catch early signs of wear.
Is it possible to perform concrete repairs without professional help?
Minor surface cracks or small patches can often be addressed with DIY kits. However, for structural concerns or larger-scale damage, hiring a professional ensures long-term durability, proper curing, and code compliance.
What is the typical cost of commercial concrete repair?
Costs vary widely based on the extent and type of damage. On average, repairs range from $2 to $15 per square foot. For accurate budgeting, it’s recommended to obtain a tailored quote based on an on-site evaluation.
How long can I expect concrete repairs to last?
Well-executed repairs generally last between 5 and 10 years, especially when paired with ongoing maintenance like sealing and proper drainage management.
Will I need to close off my lot during repairs?
Most commercial concrete repairs require a curing period of 24 to 72 hours. Professional contractors often work in phases or during off-hours to minimize disruptions to your business operations.
What are the risks of neglecting damaged concrete?
Failing to address issues like cracking, spalling, or uneven slabs can result in significant structural damage. This may create trip hazards, reduce property value, and lead to complete slab replacement, often costing up to ten times more than timely repairs.
Protect Your Property and Preserve Its Value
Your commercial concrete isn’t just a foundation, it’s a reflection of your business. In Colorado’s demanding climate, environmental stress and high usage accelerate surface wear. Visible signs such as cracking, surface flaking, or pooling water shouldn’t be ignored. Early intervention helps you avoid costly overhauls, ensures a safer environment, and maintains a professional image for your property.
Be proactive. Schedule a professional assessment at www.asphaltcoatingscompany.com and invest in repairs that protect your property and your reputation.